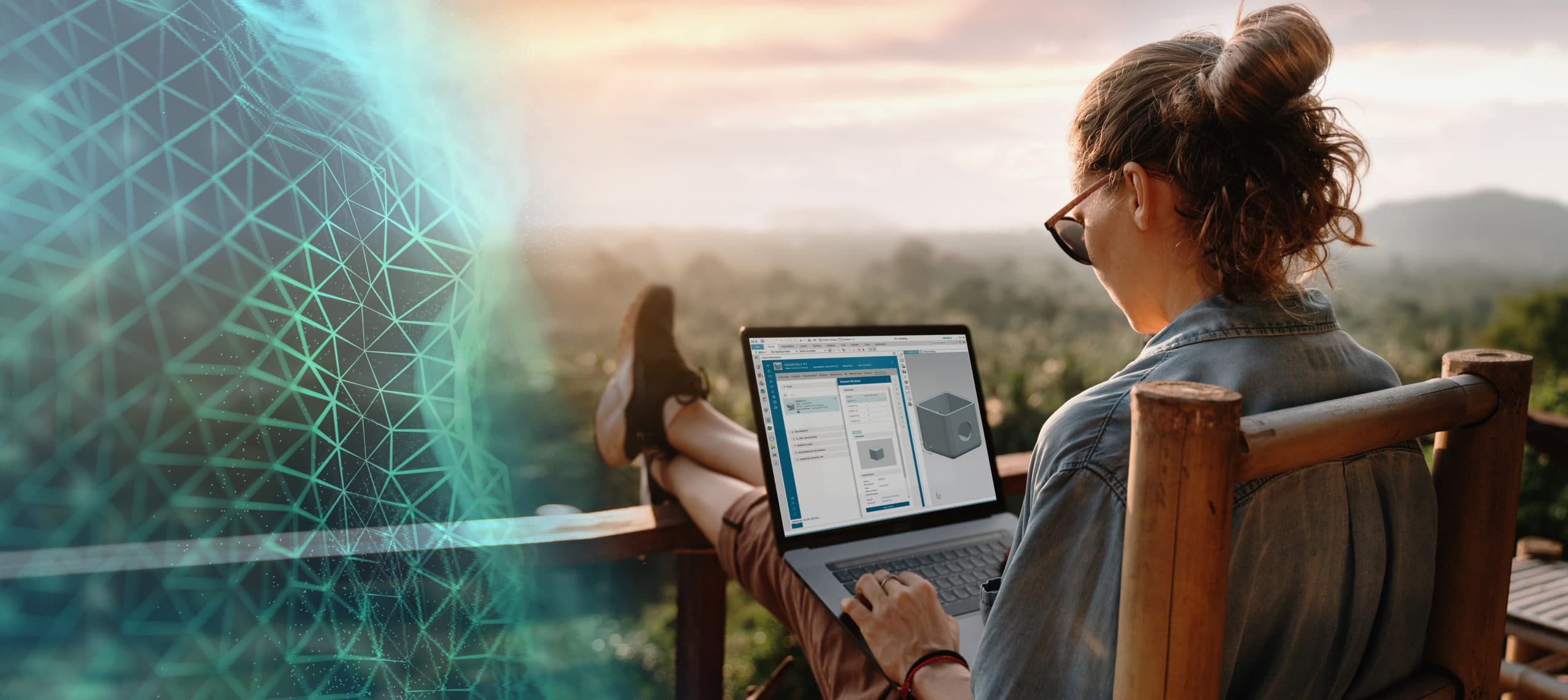
In today’s fast-paced industrial landscape, companies rely on software to manage the complexity of product development, from design through manufacturing and beyond. Teamcenter, a leading Product Lifecycle Management (PLM) platform from Siemens, is the backbone for many organizations to streamline these processes.
For IT and engineering professionals—or those studying to enter these fields—understanding Teamcenter is crucial. Even more, becoming a Teamcenter Administrator opens a world of career opportunities, especially as industries increasingly adopt PLM systems.
In this guide, we’ll dive into what Teamcenter is, how it integrates with key business functions, and why becoming a Teamcenter Administrator could be a game-changing career decision.
What is Teamcenter?
At its core, Teamcenter is a Product Lifecycle Management (PLM) software solution designed to help companies manage all aspects of a product’s life, from initial concept through design, engineering, manufacturing, and even service and disposal.
In other words, it acts as a central hub where product-related data is stored and managed across various departments and locations, ensuring that everyone involved in a product’s lifecycle has access to the most current information.
Teamcenter supports key functions such as:
- Data Management: Centralized control of CAD models, technical drawings, specifications, and documentation.
- Process Management: Orchestrating workflows across engineering, manufacturing, and supply chain teams.
- Collaboration: Enabling collaboration between teams in different locations by sharing product data in real-time.
- Compliance and Quality: Tracking regulatory requirements and ensuring product quality standards are met.
How Teamcenter Integrates with Engineering, CAD, Supply Chain, and Manufacturing
Teamcenter plays a vital role in connecting various aspects of product development and operations, making it a crucial system for industries that deal with complex products and manufacturing processes.
1. Engineering & CAD Integration
One of the main advantages of Teamcenter is its deep integration with Computer-Aided Design (CAD) systems, such as Siemens NX, SolidWorks, and AutoCAD. This allows engineers to manage CAD files, drawings, and 3D models within the Teamcenter environment. Engineers can work on designs, while the system manages version control, approvals, and product data throughout the development process.
Key Benefits:
- Manage CAD data efficiently.
- Ensure the latest version of designs is accessible to all stakeholders.
- Automate change management, preventing design errors.
2. Supply Chain
In addition to its engineering capabilities, Teamcenter provides tools for managing the supply chain by linking product data with suppliers and manufacturing partners. Teamcenter can share essential information about materials, production timelines, and technical specifications with suppliers to ensure smooth operations.
Key Benefits:
- Provide real-time updates to suppliers on part specifications.
- Track supplier performance and quality metrics.
- Enable early supplier involvement in product design.
3. Manufacturing
Teamcenter extends its capabilities to the manufacturing process, ensuring that designs created by engineering teams translate correctly to production. It allows manufacturers to create process plans, bill of materials (BOM), and work instructions based on the latest CAD data, ensuring there’s no miscommunication between engineering and production.
Key Benefits:
- Automate the transfer of engineering data to manufacturing.
- Create work instructions directly from 3D CAD models.
- Synchronize manufacturing BOMs with design BOMs to ensure consistency.
Core Competencies of a Teamcenter Administrator
A Teamcenter Administrator is a pivotal role in any organization that uses the platform. They are responsible for maintaining the system, ensuring smooth operation, and optimizing workflows. If you’re considering this career, here are the key competencies you’ll need:
- System Configuration and Customization: Configure user permissions, workflows, and data management rules to tailor the system to company needs.
- Data Management: Ensure data integrity, manage storage solutions, and handle backups.
- System Maintenance and Upgrades: Apply software updates, patches, and troubleshoot issues.
- Integration with Other Systems: Bridge Teamcenter with ERP, MES, or CAD applications.
- User Training and Support: Train users, resolve access issues, and troubleshoot workflow problems.
The Impact of Teamcenter on Product Development
Teamcenter’s real power lies in its ability to streamline product development, improve communication across departments, and reduce errors. This impacts the final product in significant ways:
- Improved Collaboration: Everyone has access to the same up-to-date product data, improving collaboration and reducing the risk of errors.
- Reduced Time-to-Market: By automating manual tasks, Teamcenter speeds up product development, helping companies bring products to market faster.
- Enhanced Product Quality: Teamcenter ensures that all product data is accurate and up-to-date, improving quality and reducing costly rework.
- Regulatory Compliance: Teamcenter helps ensure products meet industry standards and legal requirements, reducing compliance risks.
Conclusion: Why Become a Teamcenter Administrator?
As companies adopt more digital tools and PLM systems to manage complex product data, the role of a Teamcenter Administrator is becoming more critical. By mastering its core competencies, you position yourself at the heart of a company’s product development and manufacturing processes.